Maximizing the potential of DXF format in digital engineering and automation
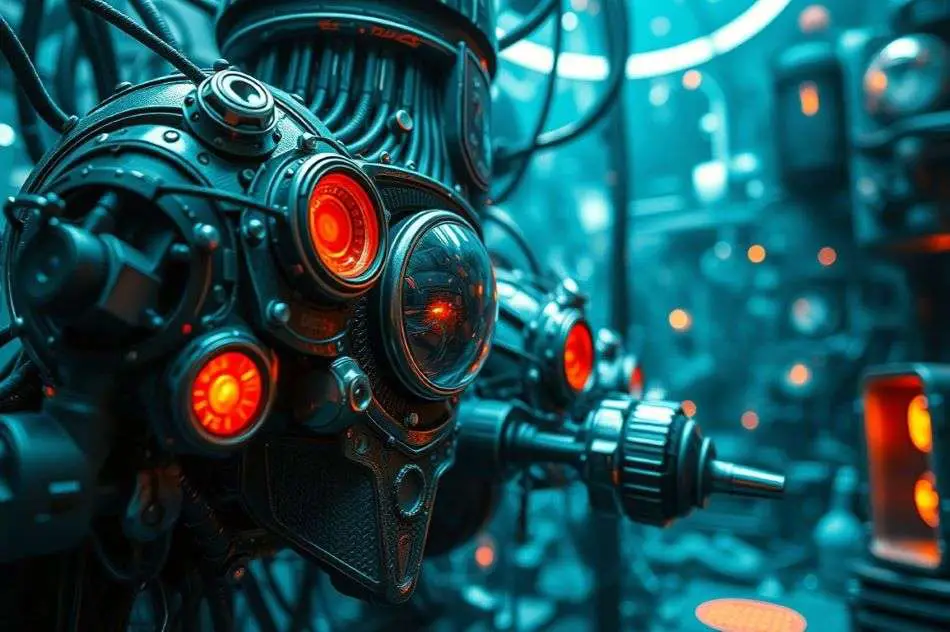
In the always-changing fields of digital engineering and automation, efficient and precise design tools are critical. One such tool that has become essential in various industries is the DXF Format (Drawing Exchange Format). Originally developed by Autodesk for AutoCAD, this versatile format has become a key resource in engineering workflows, CAD systems, and automated production processes.
This article explores how DXF is transforming engineering, automation, and manufacturing. Special attention is given to its practical applications, such as creating Professional Outdoor Fireplace Blueprints, along with its role in product design, architecture, robotics, AI-powered optimization, and efficient production workflows.
What Is the DXF format and why is it important in modern engineering?
DXF is an open, widely adopted file format that ensures seamless data exchange between different design platforms. It can store both 2D and 3D geometric data, along with metadata like layer assignments, text annotations, and object properties, making it a versatile tool for engineers and designers.
In automation, DXF simplifies the transition from digital design to manufacturing systems, ensuring precision and efficiency. Its capability to transfer intricate design details without loss of accuracy makes it an indispensable tool for industries such as architecture, automotive, aerospace, and consumer product development. For example, it is ideal for producing Professional Outdoor Fireplace Blueprints, where precision and customization are essential.
How DXF is transforming engineering and manufacturing workflows
Improving CAD systems and precision engineering
In CAD workflows, DXF files enable the creation of detailed blueprints and designs that can be directly fed into CNC machines, 3D printers, and laser cutters. This ensures that digital models are translated into physical components with high precision.
For example, DXF files are often used to design Professional Outdoor Fireplace Blueprints. These blueprints can then be sent directly to CNC routers or laser cutters, ensuring that each component is fabricated to exact specifications. This not only enhances design accuracy but also streamlines the production process.
Streamlining automated manufacturing
DXF files play a vital role in automated manufacturing by acting as a bridge between design and production. Their compatibility with CNC machines, robotic systems, and additive manufacturing tools ensures that production equipment operates based on precise design data, minimizing errors and manual intervention.
In projects like fabricating outdoor fireplaces, DXF files enable seamless production of components, ensuring perfect alignment and compatibility during assembly. The format’s ability to store both 2D and 3D data makes it ideal for such projects, where both structural integrity and aesthetic design are crucial.
AI-driven Design optimization
AI and machine learning technologies are increasingly integrated with DXF data to optimize designs. AI algorithms can analyze DXF files to suggest improvements, identify weak points, and minimize material waste. For example, they can recommend the most efficient way to cut materials when producing customized outdoor fireplace components, reducing costs and production time.
This combination of AI-driven insights and DXF precision is particularly valuable in creating Professional Outdoor Fireplace Blueprints, where optimization can enhance both design quality and sustainability.
Supporting 3D printing and rapid prototyping
The DXF format is critical for 3D printing and prototyping, enabling engineers to quickly transition from digital designs to physical models. In the case of outdoor fireplaces, DXF files can be used to create intricate, customized components, ensuring a perfect fit and high-quality finish.
By converting CAD designs into DXF format, engineers can send their blueprints directly to additive manufacturing systems, reducing the time and effort required for prototyping. This approach accelerates the development cycle and allows for rapid adjustments based on customer feedback or functional testing.
Applications of DXF across engineering disciplines
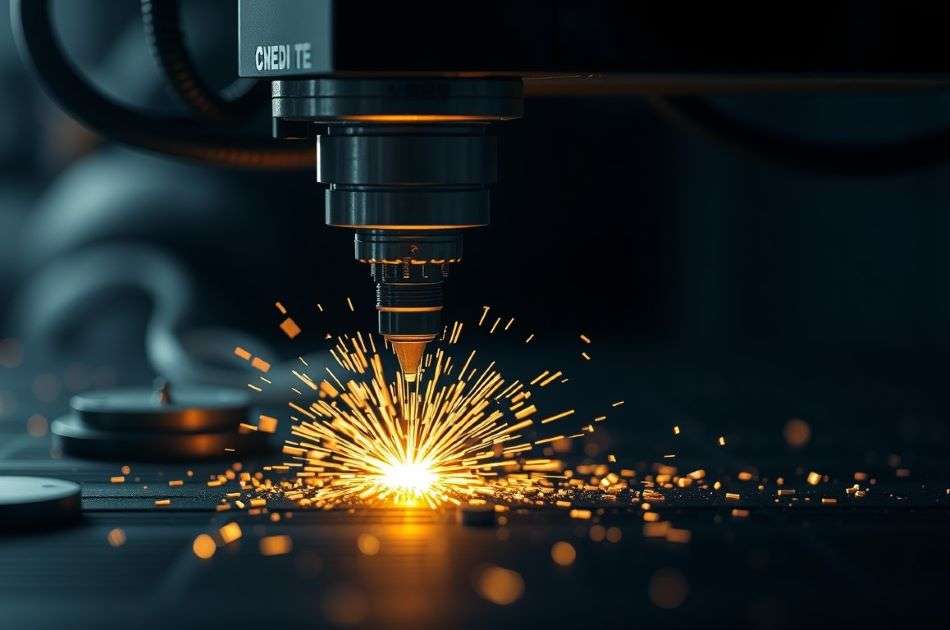
Architecture and Construction
DXF is widely used in architecture and construction to create blueprints and detailed plans. For outdoor installations, such as fireplaces, the format allows for modular and customizable designs that meet client specifications. Once finalized, the DXF file is sent directly to CNC machines or laser cutters to fabricate the components, ensuring precision and efficiency throughout the production process.
Robotics and Automated Systems
In robotics, DXF files are instrumental in designing and manufacturing parts with precision. Robotic systems rely on the detailed geometric data stored in DXF files to perform tasks such as cutting, welding, and assembling components. For example, in projects involving outdoor fireplaces, robotic welding systems can use DXF files to ensure consistent quality and alignment during assembly.
The future of DXF in engineering and automation
As automation and AI technologies continue to advance, the role of DXF will only grow. Its ability to seamlessly connect design and production processes makes it an essential tool for engineers and manufacturers. Projects like Professional Outdoor Fireplace Blueprints showcase how DXF can bridge the gap between creativity and precision, delivering customized solutions with minimal effort.
By integrating AI-driven design, robotic automation, and digital manufacturing workflows, industries can unlock new levels of efficiency and innovation. The DXF format enables engineers to streamline their workflows and achieve precise results, whether for large-scale industrial applications or highly customized designs.
Conclusion
The DXF format is more than just a tool for drawing—it is a cornerstone of digital engineering and automated manufacturing. From CAD design to AI-powered optimization, it supports efficiency, accuracy, and innovation across industries.
Applications such as Professional Outdoor Fireplace Blueprints demonstrate its versatility, providing an efficient way to translate detailed designs into precise physical components. By understanding its full potential, engineers and manufacturers can optimize workflows, reduce costs, and accelerate time-to-market. The DXF format will continue to play a vital role in the future of engineering, bridging the gap between imagination and reality.